What is Porosity in Welding: Understanding Its Causes and Enhancing Your Skills
What is Porosity in Welding: Understanding Its Causes and Enhancing Your Skills
Blog Article
The Science Behind Porosity: A Comprehensive Overview for Welders and Fabricators
Understanding the detailed devices behind porosity in welding is vital for welders and producers striving for impeccable workmanship. From the composition of the base materials to the details of the welding procedure itself, a multitude of variables conspire to either exacerbate or relieve the existence of porosity.
Understanding Porosity in Welding
FIRST SENTENCE:
Assessment of porosity in welding exposes critical understandings right into the integrity and high quality of the weld joint. Porosity, defined by the visibility of tooth cavities or voids within the weld metal, is a typical problem in welding processes. These gaps, if not correctly attended to, can jeopardize the architectural honesty and mechanical homes of the weld, leading to prospective failings in the completed item.
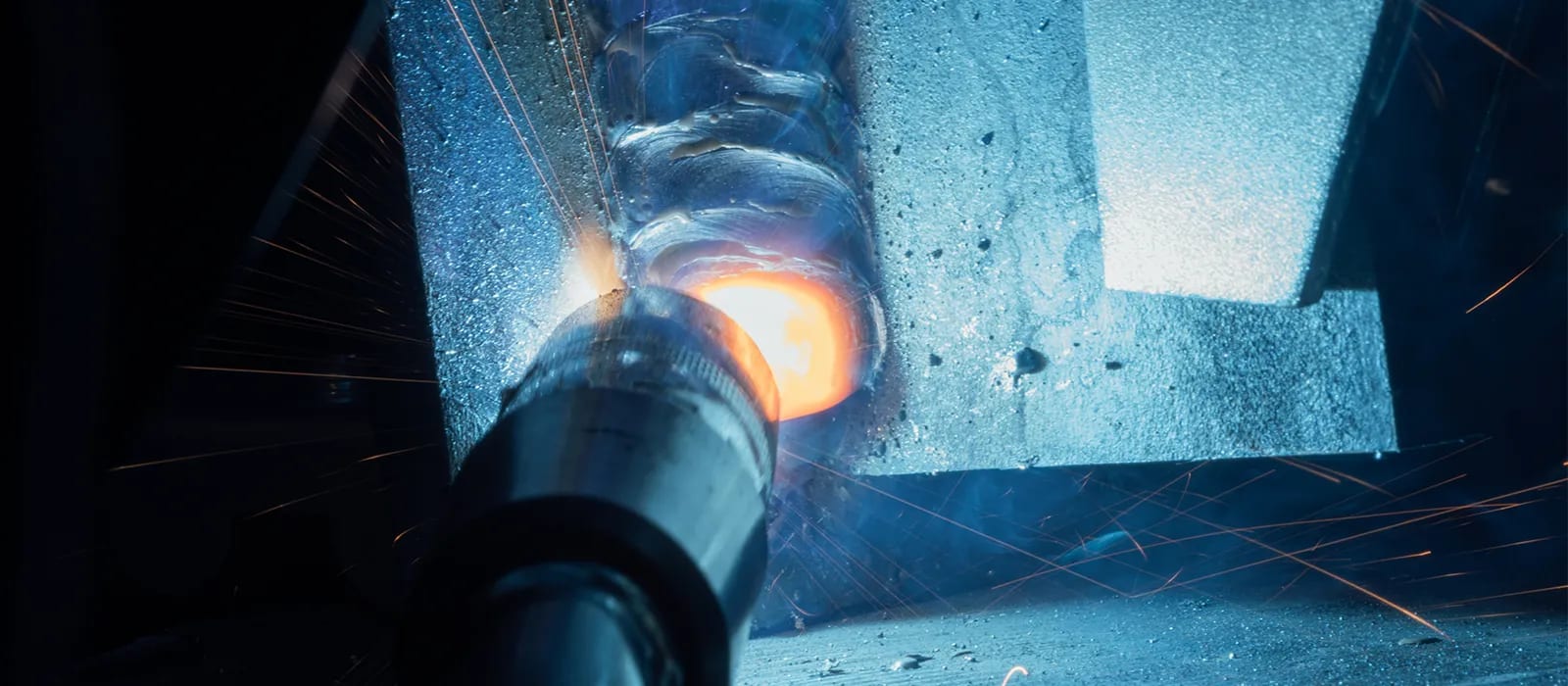
To find and quantify porosity, non-destructive screening approaches such as ultrasonic testing or X-ray assessment are typically used. These techniques permit the identification of inner defects without compromising the honesty of the weld. By analyzing the dimension, form, and circulation of porosity within a weld, welders can make informed decisions to improve their welding processes and achieve sounder weld joints.

Aspects Influencing Porosity Formation
The event of porosity in welding is influenced by a myriad of variables, ranging from gas shielding performance to the ins and outs of welding parameter setups. Welding criteria, consisting of voltage, existing, take a trip speed, and electrode kind, likewise influence porosity formation. The welding technique utilized, such as gas metal arc welding (GMAW) or protected metal arc welding (SMAW), can influence porosity development due to variations in warmth circulation and gas protection - What is Porosity.
Impacts of Porosity on Weld Quality
The existence of porosity likewise weakens the weld's resistance to corrosion, as the trapped air or gases within the spaces can react with the surrounding atmosphere, leading to degradation over time. Additionally, porosity can impede the weld's capacity to hold up against stress or influence, more threatening the general find out this here high quality and reliability of the bonded structure. In crucial applications such as aerospace, automotive, or architectural buildings, where safety and toughness are paramount, the detrimental impacts of porosity on weld quality can have serious effects, emphasizing the value of decreasing porosity with proper welding techniques and procedures.
Methods to Lessen Porosity
To enhance the quality of bonded joints and guarantee architectural honesty, welders and producers utilize particular methods targeted at decreasing the formation of gaps and tooth cavities within the material throughout the welding process. One reliable method to minimize porosity is to guarantee correct product prep work. This includes complete cleansing of the base metal to remove any type of pollutants such as oil, oil, or moisture that might add to porosity formation. Additionally, using the appropriate welding parameters, such as the appropriate voltage, present, and travel rate, is important in avoiding porosity. Preserving a consistent arc length and angle during welding also assists decrease the probability of porosity.

Additionally, selecting the ideal protecting gas linked here and maintaining appropriate gas circulation prices are necessary in lessening porosity. Making use of the appropriate welding method, such as back-stepping or employing a weaving activity, can likewise assist disperse heat evenly and decrease the possibilities of porosity development. Ensuring appropriate air flow in the welding atmosphere to eliminate any kind of potential sources of contamination is vital for accomplishing porosity-free welds. By carrying out these strategies, welders can properly decrease porosity and produce high-grade welded joints.
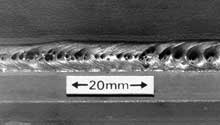
Advanced Solutions for Porosity Control
Executing sophisticated modern technologies and innovative methods plays a pivotal function in achieving premium control over porosity in welding processes. One innovative service is making use of sophisticated gas combinations. Securing gases like helium or a mix of argon and hydrogen can help in reducing porosity by offering far better arc security and enhanced gas insurance coverage. Additionally, utilizing advanced welding Full Report methods such as pulsed MIG welding or customized atmosphere welding can likewise aid reduce porosity concerns.
One more advanced option includes using sophisticated welding tools. Making use of equipment with integrated attributes like waveform control and advanced power sources can improve weld high quality and reduce porosity dangers. The execution of automated welding systems with accurate control over specifications can considerably decrease porosity flaws.
Moreover, integrating innovative monitoring and assessment modern technologies such as real-time X-ray imaging or automated ultrasonic screening can aid in detecting porosity early in the welding procedure, enabling instant corrective activities. On the whole, integrating these advanced remedies can considerably improve porosity control and boost the general high quality of bonded components.
Conclusion
In conclusion, recognizing the scientific research behind porosity in welding is vital for welders and fabricators to create premium welds - What is Porosity. Advanced remedies for porosity control can better enhance the welding process and make sure a strong and reputable weld.
Report this page